可搬型デパレタイザとは、従来のように床に固定せず、現場のレイアウトや荷量の変化に応じて柔軟に移動・運用できる新しいタイプの物流ロボットです。
この仕組みは、2024年にイオン福岡XDへ導入されたセンコーの実例を皮切りに、物流現場における「固定設備の限界」を打破する新たな選択肢として注目を集めています。
本記事では、日経ロボティクス5月号に掲載された「Telexistenceが開発した可搬型デパレタイザの特徴や導入背景、センコーが実運用を行う現場での効果」について詳しく解説していきます。
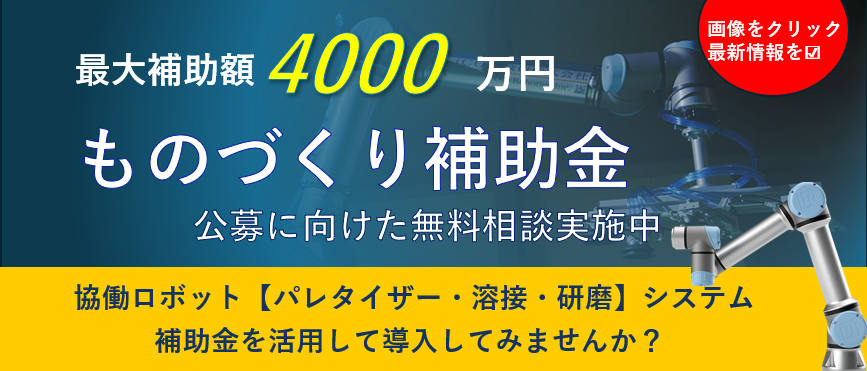
目次[]
なぜ今、可搬型デパレタイザが注目されるのか
物流業界では人手不足とコスト上昇が深刻な課題となっています。特に倉庫作業におけるパレットからの荷下ろし(デパレタイジング)は、繰り返し作業かつ重量物を扱うため、自動化のニーズが高まっています。しかし、従来の自動化設備は“動かせない”という制約があり、荷量や作業エリアの変化に柔軟に対応できませんでした。
こうした背景の中、Telexistenceが開発した可搬型デパレタイザは、「動かせる物流ロボット」という新しい選択肢を提示。設備の制約を超えて、現場主導での自動化を可能にします。2024年、センコーがイオン福岡XDにて実際に導入したこのシステムは、まさにその実現例といえるでしょう。
現場で浮かび上がる「動かせない設備」の課題
多くの物流センターでは、固定されたデパレタイザが導入されてきました。一度床にアンカーボルトで設置すれば、簡単には動かせません。その結果、次のような課題が顕在化していました。
たとえば、拠点内の荷量が偏ると、設備の稼働率が下がります。また、センター全体のレイアウト変更や拠点統廃合の際には、設備そのものが“足かせ”になるケースもあります。機器を再設置するには多大なコストと時間が必要で、現場にとっては「導入そのものが重荷」と感じられる場面も少なくありませんでした。
解決策:Telexistenceの可搬型デパレタイザが示す“新しい運用の形”
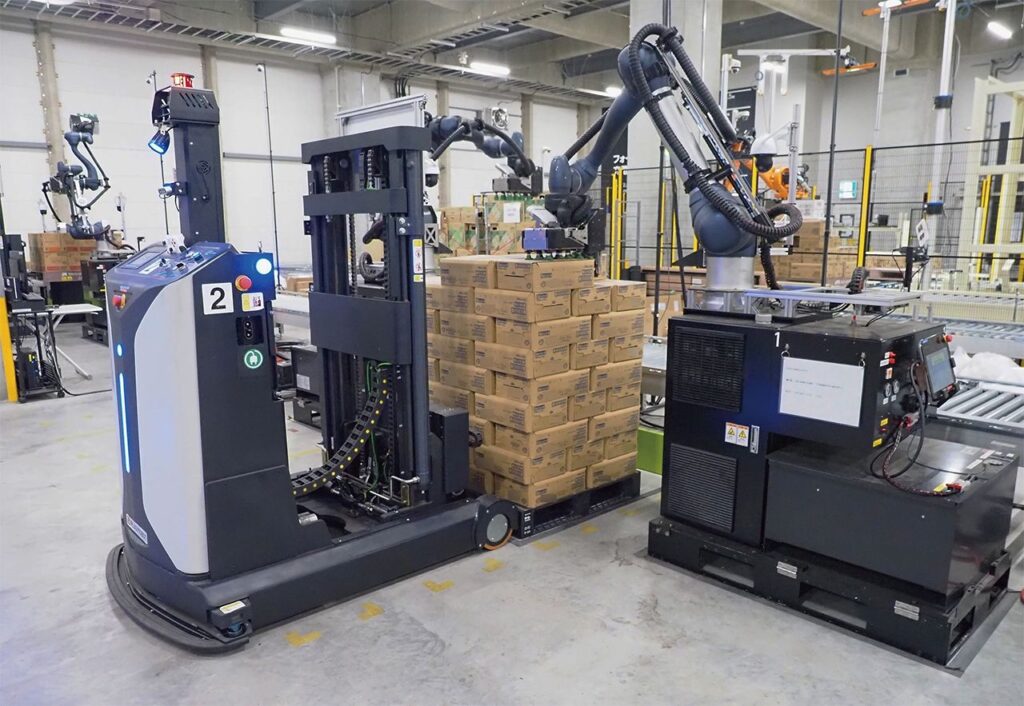
2025.04.10
特徴①:現場に応じて“動かせる”柔軟性
Telexistenceの可搬型デパレタイザは、ロボットを床に固定するのではなく、AGF(自動フォークリフト)で簡単に持ち上げて別の作業場所へ移動できる構造です。アーム本体・吸着コンプレッサーともに内蔵バッテリー駆動で、電源ケーブルは一切不要。夜間に充電するだけで日中はフル稼働が可能です。
これにより、1拠点で複数の作業エリアに対してロボットを回して使う運用が可能となり、導入設備の費用対効果を飛躍的に向上させます。
特徴②:導入から運用まで“無理のない仕組み”
このロボットはRaaS(Robot as a Service)モデルで提供されており、高額な初期投資が不要です。また、複数のカメラを活用した遠隔オペレーション体制が整っており、例外的なケース(たとえば吸着失敗など)も、遠隔からTelexistenceのオペレーターが即時に対応する仕組みになっています。
そのため、現場の作業者がロボットの異常対応に追われることはなく、安心して現場にロボットを配置できます。
導入効果:福岡のセンターで見えた現実的メリット
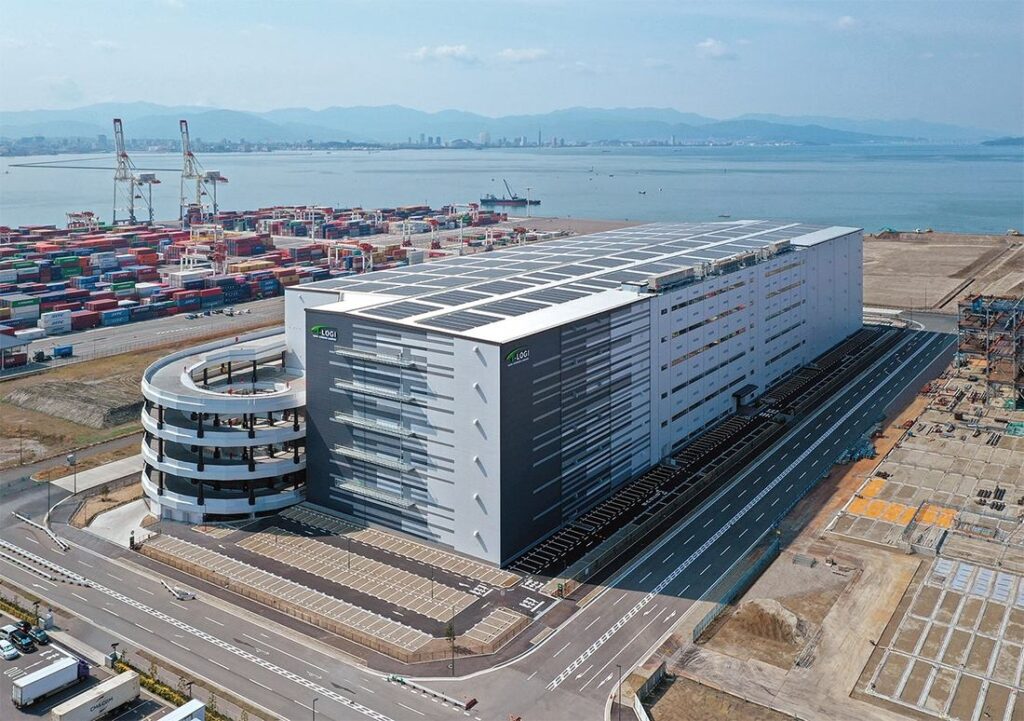
2025.04.10
センコーが導入したイオン福岡XDでは、4台の可搬型デパレタイザと4台のAGFが稼働中。この構成で、1日あたり数千ケースに及ぶ処理を自動化しています。
特筆すべきは、「1パレットに対して2台のロボットが左右から同時に作業」する構成。これによりスループットを最大化しつつ、コンパクトな設置面積を維持。安全柵の不要な設計により、人の導線とも両立した柔軟なレイアウトが可能になりました。
さらに、荷下ろしが進んでパレット上のケースが減少した場合でも、AGFがパレット自体を持ち上げて高さを調整することで、アームが最後まで作業できるように設計されています。こうしたロボットと搬送機器の協調動作が、業務の中断を防ぎ、安定した自動化を実現しています。
現場の稼働フロー
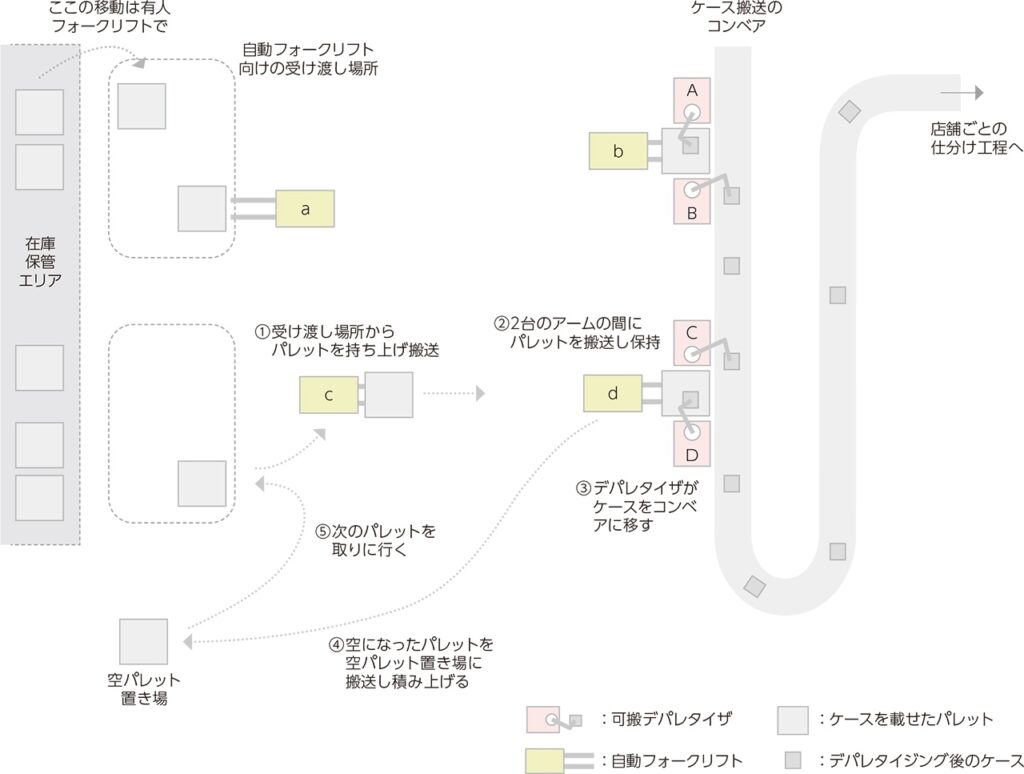
2025.04.10
本システムでは、パレットからケースを取り出す「デパレタイジングステーション」がコンベアに沿って2カ所設置されています。各ステーションでは、1つのパレットに対して2台の協働ロボットが左右から同時に作業を行います。
パレットの搬送は自動フォークリフト(AGF)が行い、各ステーションには2台のAGFが割り当てられています。
- 1台目のAGF:ステーションに設置されたパレットの横で、ロボットと連携しながらデパレタイジング作業を補助します。
- 2台目のAGF:あらかじめ定められた「受け渡し場所」から、ケースを積んだ新しいパレットをステーションへ搬送します。
デパレタイジングが進むにつれて、パレット上のケースの高さが低くなり、協働ロボットのリーチでは届かなくなる場合があります。その際には、AGFがパレットを持ち上げ、ロボットの可動範囲に高さを合わせて作業を継続します。
作業が完了した空パレットもAGFが回収し、決められた置き場まで自動で運びます。
なお、パレットは物流センターの奥に保管されており、奥から受け渡し場所までは人手によるフォークリフトで搬送されます。AGFはその受け渡し場所からパレットを受け取り、ステーションへ運搬します。
全自動化の理想と現実──費用対効果を見極めた自動化戦略の必要性
Telexistenceの可搬型デパレタイザは、物流自動化における革新的な一手であり、特に大規模な物流拠点においては高い効果が期待できます。しかし、すべての現場に最適とは限らないというのが、私たちが現場で培ってきた実感です。
もちろん、全自動化による作業負担軽減や処理能力向上は大きな魅力です。しかしその一方で、ズレのない精密な位置決めや完全にフラットな床面の確保といった高度な環境整備が求められ、システム導入には相応の初期投資と維持管理コストがかかります。
さらに重要なのは、こうした全自動化設備の費用対効果を回収できるだけの処理数があるかどうかという点です。特に、人手不足が深刻でありながらもスペースや処理数に限りのある食品工場や中小規模倉庫では、全自動化が過剰投資となるケースも少なくありません。
全自動化システムは、周辺の搬送設備や倉庫管理システムと連動させて初めて真価を発揮します。言い換えれば、設備全体として自動化を統合しなければシナジー(相乗効果)は生まれないということです。そのため、導入効果を最大化するには、物流量が安定し、かつ長期的な運用が見込める現場でこそ適しているといえるでしょう。
準完全自動化というもう一つの最適解──協働ロボットの実力
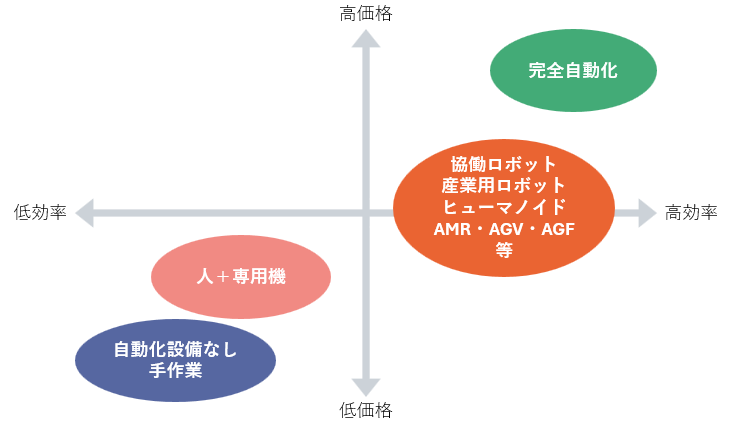
一方で、大規模な物流倉庫を除く多くの現場では、環境整備やシステム全体の構築に莫大なコストをかけられないという現実があります。
そのうえで、自動化において本当に求められるのは、サイクルタイムの改善や積み付け高さの向上など、限られた投資で高い効果が期待できる設備です。
私たちが推進している協働ロボットによる準自動化(ピンポイント自動化)は、まさにこうしたニーズに応える現実的かつ柔軟な選択肢です。
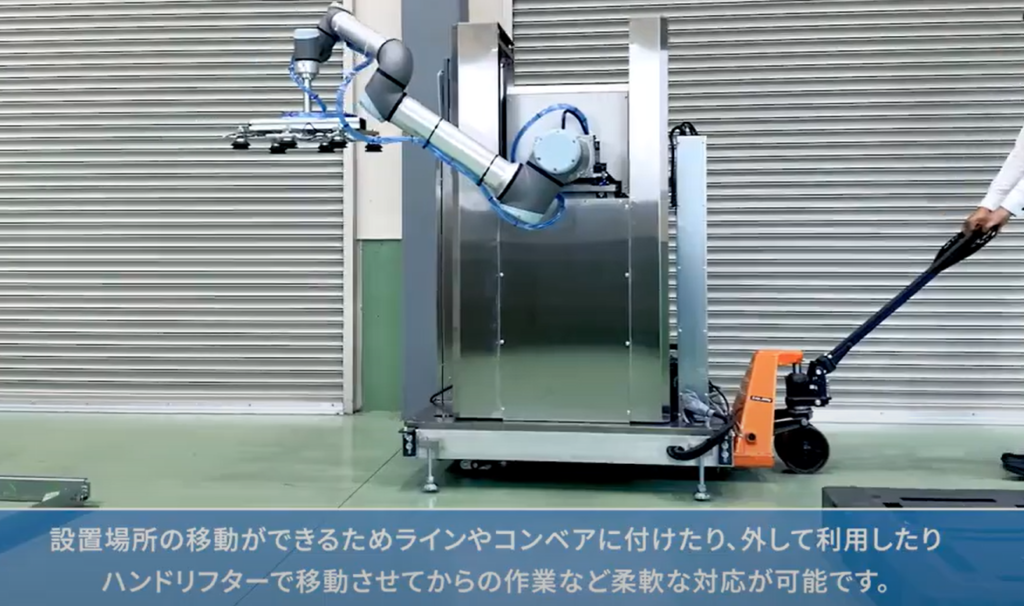
たとえば弊社の協働ロボットは、ハンドフォークなどで簡単に移動可能であり、電源工事や固定設置を必要としない可搬性を備えています。これは、固定設備がレイアウト変更や設備移設の障壁となる従来課題に対する、明確な解決策です。
また、省スペースで導入できるため、既存ラインに組み込む形での部分的な自動化が可能です。工程ごとに「人の負担が大きい作業」を見極め、そこに協働ロボットを適用することで、限られた投資でも確実に効果が見込めるのです。
さらに、サイクルタイムの改善や積み付け高さへの対応といった、具体的な物流効率への貢献も見逃せません。
積み付け効率から見る導入効果──輸送効率の最大化
近年注目されている“物流2024年問題”では、ドライバー不足や法改正への対応が急務とされています。その中で特に重要視されているのが、輸送効率の向上=1回の積載量の最大化です。
10tトラックの内高は約2.6m。人手による積み付けでは1.5m程度が限界ですが、弊社協働ロボットシステムは最大2.1mの積み付けに対応しており、他社の標準的な1900mmよりも高い積載が可能です。
これにより、1回の輸送あたりの搬送量が大幅に増加し、燃料費の削減や車両回転率の向上にもつながります。
このような要素は、“単なる機械導入”ではなく、“全体最適に貢献する機器選定”の視点が必要であることを示しています。
導入効果の鍵は「積み付け高さ」と「サイクルタイム」
加えて、限られたスペースでの設置や運用にも適しており、既存設備を大きく変更せずに省スペースかつ短期間で自動化が可能です。これにより、処理数の大小にかかわらず、中小規模の倉庫でも導入しやすい柔軟な選択肢となっています。
私たちは、現場ごとに最適な“ピンポイント自動化”を推進しています。重要なのは、単に“技術が高い”ことではなく、それが現場運用とどれだけ噛み合っているか。コストを抑えながら、確実に効果を出せる部分から導入できるのが、協働ロボットの最大のメリットです。
現場を知るプロフェッショナルとしての提案
自動化を進める際に最も重要なのは、「最新技術を入れること」ではなく、「現場の課題に合った自動化を選ぶこと」です。
大規模物流拠点ではフルオート、変動の大きい現場では柔軟なピンポイント自動化。このすみ分けこそが、現代の自動化戦略に必要な視点です。
私たちiCOM技研は、協働ロボットの強みを最大限に活かしながら、過剰な投資を避け、現場に根ざした導入効果を最大化するご提案を行っています。
お客様の課題に寄り添い、最も効果的な自動化の形をともに設計いたします。。
まとめと今後の展望:物流の“設計思想”が変わる
Telexistenceの可搬型デパレタイザは、物流現場に「動かせる設備」という新しい常識をもたらしました。これは単なる構造の変化ではなく、運用設計そのものを柔軟にする発想の転換です。
今後は、複数の品種が混在した“混載パレット”への対応も視野に入れており、さらなる進化が期待されます。
「必要なときに、必要な場所に、最小限の投資でロボットを導入する」。そんな理想的な物流自動化の未来を、現実のものとして示してくれる事例です。
可搬型=“使い回せる設備”という発想の転換
従来の考え方では、設備とは「導入したらその場で動かすもの」でした。
しかし、荷量や人の配置が日々変化する物流現場においては、“使わない時間や場所”が必ず発生します。
Telexistenceの可搬型デパレタイザは、そんな“非稼働時間”を極力減らす思想のもとで開発されています。自動フォークリフトで簡単に移動・再設置ができる構造と、バッテリー駆動によるコードレス設計により、今までにない「設備の運用自由度」が現場にもたらされます。
この考え方は、私たちが提供する協働ロボットシステムとも非常に親和性が高く、
“工程単位の省力化”から“拠点全体のフレキシブル運用”へと、自動化の概念自体を広げるものです。
iCOM技研が考える、“現場に最適な自動化”とは
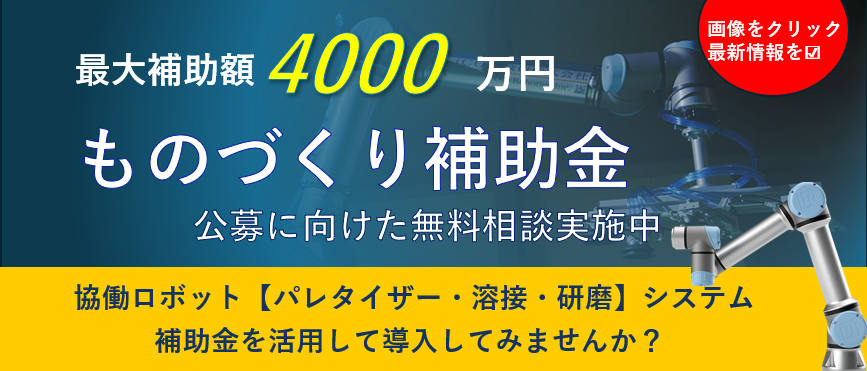
自動化において重要なのは、「技術の高さ」ではなく「運用との適合性」です。いくら高度な技術であっても、それが現場に合わなければ真の効果は生まれません。
協働ロボットは、ピッキング、積み付け、仕分け、検査などさまざまな工程で活用されており、今回の可搬型デパレタイザのように、既存の自動化設備の構成要素としても組み込むことが可能です。
私たちは、省人化と柔軟性のバランスを取る現場最適化型の自動化提案を強みとしています。固定でもフルオートでもない、「現場に合わせて動かせるロボット」という新しい考え方を、今後も広く提案してまいります。